Common Production Processes for Chip Resistors
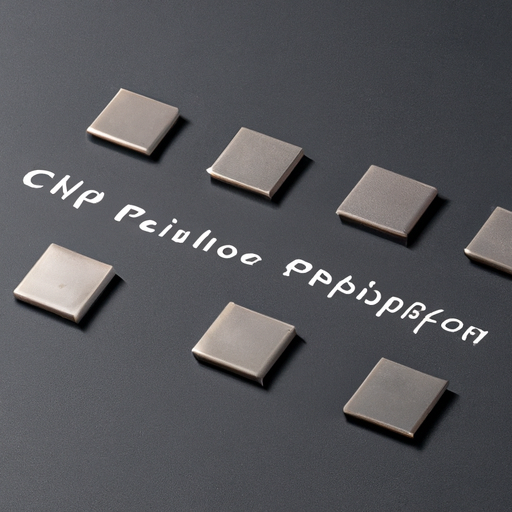
I. Introduction
Chip resistors are essential components in modern electronic circuits, serving the critical function of controlling current flow and voltage levels. These tiny devices, often measuring just a few millimeters in size, are ubiquitous in a wide range of applications, from consumer electronics to industrial machinery. Understanding the production processes behind chip resistors is vital for engineers, manufacturers, and anyone interested in the electronics industry. This blog post will explore the common production processes for chip resistors, detailing the types of resistors, raw materials, manufacturing techniques, quality control measures, and future trends in the industry.
II. Types of Chip Resistors
A. Thin Film Resistors
Thin film resistors are characterized by a thin layer of resistive material deposited on a substrate. They offer high precision and stability, making them ideal for applications requiring tight tolerances, such as in medical devices and aerospace electronics.
B. Thick Film Resistors
Thick film resistors, on the other hand, are made by printing a thicker layer of resistive paste onto a substrate. They are more cost-effective than thin film resistors and are widely used in consumer electronics, automotive applications, and power circuits.
C. Other Types
In addition to thin and thick film resistors, there are other types, such as metal film resistors, which provide excellent stability and low noise, and wirewound resistors, known for their high power handling capabilities. Each type has its unique characteristics and applications, catering to various needs in the electronics market.
III. Raw Materials Used in Chip Resistor Production
A. Substrates
The choice of substrate is crucial in chip resistor production. Common materials include:
1. **Ceramic Materials**: These are widely used due to their excellent thermal stability and electrical insulation properties.
2. **Glass and Polymer Substrates**: These materials are also used, particularly in applications where flexibility or transparency is required.
B. Conductive Materials
The resistive element is created using various conductive materials:
1. **Metal Pastes for Thick Film**: These pastes typically contain a mixture of metal oxides and glass frit, allowing for easy application and good adhesion to substrates.
2. **Thin Film Materials**: Metals such as nickel, gold, and tantalum are commonly used in thin film resistors, providing high precision and stability.
C. Dielectric Materials
Dielectric materials are essential for insulating layers and protective coatings. They help prevent electrical leakage and enhance the durability of the resistors.
IV. Common Production Processes
A. Design and Prototyping
The production of chip resistors begins with careful design and prototyping. Engineers must consider circuit design, resistance values, and tolerance levels. Prototyping methods, such as 3D printing or rapid prototyping, allow for quick iterations and testing of designs before full-scale production.
B. Substrate Preparation
Once the design is finalized, substrate preparation begins. This involves:
1. **Cleaning and Surface Treatment**: Substrates must be thoroughly cleaned to remove any contaminants that could affect adhesion and performance.
2. **Cutting and Shaping Substrates**: Substrates are cut to the desired dimensions, ensuring they fit the specifications of the final product.
C. Deposition Techniques
The deposition of resistive materials is a critical step in the production process.
1. **Thick Film Printing**: This process involves screen printing a thick layer of resistive paste onto the substrate. After printing, the resistors undergo drying and curing to solidify the material.
2. **Thin Film Deposition**: Techniques such as sputtering and chemical vapor deposition (CVD) are used to create thin films of resistive material. These methods allow for precise control over the thickness and uniformity of the film.
D. Resistor Patterning
After deposition, the resistive material must be patterned to create the desired resistor shape. This is typically done using:
1. **Photolithography**: A light-sensitive material is applied to the substrate, and UV light is used to expose specific areas, creating a pattern.
2. **Etching Processes**: Chemical or plasma etching removes unwanted material, leaving behind the desired resistor pattern.
E. Trimming and Tolerance Adjustment
To achieve the required resistance values, trimming is necessary. This can be done using:
1. **Laser Trimming Techniques**: A laser is used to precisely remove material from the resistor, adjusting its resistance value.
2. **Measurement and Quality Control**: After trimming, resistors are measured to ensure they meet specified tolerances.
F. Encapsulation and Coating
The final step in the production process is encapsulation and coating. This involves:
1. **Protective Coatings**: Resistors are coated with materials that protect them from environmental factors such as moisture and dust.
2. **Encapsulation Methods**: Techniques such as potting or molding are used to encapsulate the resistors, providing additional protection and stability.
V. Quality Control and Testing
Quality control is paramount in chip resistor production to ensure reliability and performance.
A. Electrical Testing
1. **Resistance Measurement**: Each resistor is tested to confirm it meets the specified resistance value.
2. **Temperature Coefficient Testing**: This test evaluates how the resistance changes with temperature, ensuring stability under varying conditions.
B. Mechanical Testing
1. **Stress and Strain Testing**: Resistors are subjected to mechanical stress to assess their durability and performance under physical strain.
2. **Environmental Testing**: This includes exposure to extreme temperatures, humidity, and other environmental factors to ensure reliability.
C. Reliability Testing
1. **Life Cycle Testing**: Resistors undergo accelerated life testing to simulate long-term use and identify potential failure modes.
2. **Accelerated Aging Tests**: These tests help predict the lifespan of resistors by exposing them to conditions that accelerate aging.
VI. Environmental Considerations
As the electronics industry evolves, so do the environmental considerations associated with chip resistor production.
A. Waste Management
1. **Recycling of Materials**: Manufacturers are increasingly focusing on recycling materials used in production to minimize waste.
2. **Disposal of Hazardous Substances**: Proper disposal methods for hazardous materials are essential to prevent environmental contamination.
B. Compliance with Regulations
1. **RoHS and WEEE Directives**: Compliance with regulations such as the Restriction of Hazardous Substances (RoHS) and Waste Electrical and Electronic Equipment (WEEE) directives is crucial for manufacturers.
2. **Environmental Certifications**: Many companies seek certifications to demonstrate their commitment to environmentally friendly practices.
VII. Future Trends in Chip Resistor Production
The chip resistor industry is poised for significant advancements in the coming years.
A. Advances in Materials Science
Research into new materials may lead to the development of resistors with improved performance characteristics, such as higher power ratings and better thermal stability.
B. Automation and Industry 4.0
The integration of automation and smart manufacturing technologies will streamline production processes, enhance efficiency, and reduce costs.
C. Miniaturization and Integration with Other Components
As electronic devices continue to shrink, the demand for smaller, more integrated components will drive innovation in chip resistor design and production.
VIII. Conclusion
In summary, chip resistors play a vital role in electronic circuits, and understanding their production processes is essential for anyone involved in the electronics industry. From the types of resistors and raw materials used to the intricate manufacturing techniques and quality control measures, each step in the production process contributes to the reliability and performance of these components. As the industry evolves, staying informed about future trends and advancements will be crucial for manufacturers and engineers alike. The future of chip resistor technology looks promising, with ongoing innovations set to enhance their capabilities and applications in the ever-evolving world of electronics.
Common Production Processes for Chip Resistors
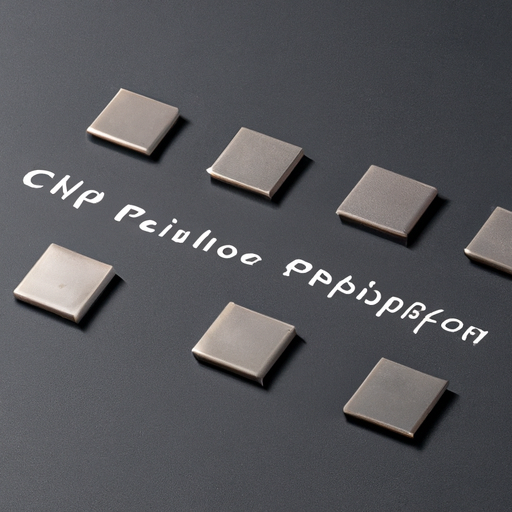
I. Introduction
Chip resistors are essential components in modern electronic circuits, serving the critical function of controlling current flow and voltage levels. These tiny devices, often measuring just a few millimeters in size, are ubiquitous in a wide range of applications, from consumer electronics to industrial machinery. Understanding the production processes behind chip resistors is vital for engineers, manufacturers, and anyone interested in the electronics industry. This blog post will explore the common production processes for chip resistors, detailing the types of resistors, raw materials, manufacturing techniques, quality control measures, and future trends in the industry.
II. Types of Chip Resistors
A. Thin Film Resistors
Thin film resistors are characterized by a thin layer of resistive material deposited on a substrate. They offer high precision and stability, making them ideal for applications requiring tight tolerances, such as in medical devices and aerospace electronics.
B. Thick Film Resistors
Thick film resistors, on the other hand, are made by printing a thicker layer of resistive paste onto a substrate. They are more cost-effective than thin film resistors and are widely used in consumer electronics, automotive applications, and power circuits.
C. Other Types
In addition to thin and thick film resistors, there are other types, such as metal film resistors, which provide excellent stability and low noise, and wirewound resistors, known for their high power handling capabilities. Each type has its unique characteristics and applications, catering to various needs in the electronics market.
III. Raw Materials Used in Chip Resistor Production
A. Substrates
The choice of substrate is crucial in chip resistor production. Common materials include:
1. **Ceramic Materials**: These are widely used due to their excellent thermal stability and electrical insulation properties.
2. **Glass and Polymer Substrates**: These materials are also used, particularly in applications where flexibility or transparency is required.
B. Conductive Materials
The resistive element is created using various conductive materials:
1. **Metal Pastes for Thick Film**: These pastes typically contain a mixture of metal oxides and glass frit, allowing for easy application and good adhesion to substrates.
2. **Thin Film Materials**: Metals such as nickel, gold, and tantalum are commonly used in thin film resistors, providing high precision and stability.
C. Dielectric Materials
Dielectric materials are essential for insulating layers and protective coatings. They help prevent electrical leakage and enhance the durability of the resistors.
IV. Common Production Processes
A. Design and Prototyping
The production of chip resistors begins with careful design and prototyping. Engineers must consider circuit design, resistance values, and tolerance levels. Prototyping methods, such as 3D printing or rapid prototyping, allow for quick iterations and testing of designs before full-scale production.
B. Substrate Preparation
Once the design is finalized, substrate preparation begins. This involves:
1. **Cleaning and Surface Treatment**: Substrates must be thoroughly cleaned to remove any contaminants that could affect adhesion and performance.
2. **Cutting and Shaping Substrates**: Substrates are cut to the desired dimensions, ensuring they fit the specifications of the final product.
C. Deposition Techniques
The deposition of resistive materials is a critical step in the production process.
1. **Thick Film Printing**: This process involves screen printing a thick layer of resistive paste onto the substrate. After printing, the resistors undergo drying and curing to solidify the material.
2. **Thin Film Deposition**: Techniques such as sputtering and chemical vapor deposition (CVD) are used to create thin films of resistive material. These methods allow for precise control over the thickness and uniformity of the film.
D. Resistor Patterning
After deposition, the resistive material must be patterned to create the desired resistor shape. This is typically done using:
1. **Photolithography**: A light-sensitive material is applied to the substrate, and UV light is used to expose specific areas, creating a pattern.
2. **Etching Processes**: Chemical or plasma etching removes unwanted material, leaving behind the desired resistor pattern.
E. Trimming and Tolerance Adjustment
To achieve the required resistance values, trimming is necessary. This can be done using:
1. **Laser Trimming Techniques**: A laser is used to precisely remove material from the resistor, adjusting its resistance value.
2. **Measurement and Quality Control**: After trimming, resistors are measured to ensure they meet specified tolerances.
F. Encapsulation and Coating
The final step in the production process is encapsulation and coating. This involves:
1. **Protective Coatings**: Resistors are coated with materials that protect them from environmental factors such as moisture and dust.
2. **Encapsulation Methods**: Techniques such as potting or molding are used to encapsulate the resistors, providing additional protection and stability.
V. Quality Control and Testing
Quality control is paramount in chip resistor production to ensure reliability and performance.
A. Electrical Testing
1. **Resistance Measurement**: Each resistor is tested to confirm it meets the specified resistance value.
2. **Temperature Coefficient Testing**: This test evaluates how the resistance changes with temperature, ensuring stability under varying conditions.
B. Mechanical Testing
1. **Stress and Strain Testing**: Resistors are subjected to mechanical stress to assess their durability and performance under physical strain.
2. **Environmental Testing**: This includes exposure to extreme temperatures, humidity, and other environmental factors to ensure reliability.
C. Reliability Testing
1. **Life Cycle Testing**: Resistors undergo accelerated life testing to simulate long-term use and identify potential failure modes.
2. **Accelerated Aging Tests**: These tests help predict the lifespan of resistors by exposing them to conditions that accelerate aging.
VI. Environmental Considerations
As the electronics industry evolves, so do the environmental considerations associated with chip resistor production.
A. Waste Management
1. **Recycling of Materials**: Manufacturers are increasingly focusing on recycling materials used in production to minimize waste.
2. **Disposal of Hazardous Substances**: Proper disposal methods for hazardous materials are essential to prevent environmental contamination.
B. Compliance with Regulations
1. **RoHS and WEEE Directives**: Compliance with regulations such as the Restriction of Hazardous Substances (RoHS) and Waste Electrical and Electronic Equipment (WEEE) directives is crucial for manufacturers.
2. **Environmental Certifications**: Many companies seek certifications to demonstrate their commitment to environmentally friendly practices.
VII. Future Trends in Chip Resistor Production
The chip resistor industry is poised for significant advancements in the coming years.
A. Advances in Materials Science
Research into new materials may lead to the development of resistors with improved performance characteristics, such as higher power ratings and better thermal stability.
B. Automation and Industry 4.0
The integration of automation and smart manufacturing technologies will streamline production processes, enhance efficiency, and reduce costs.
C. Miniaturization and Integration with Other Components
As electronic devices continue to shrink, the demand for smaller, more integrated components will drive innovation in chip resistor design and production.
VIII. Conclusion
In summary, chip resistors play a vital role in electronic circuits, and understanding their production processes is essential for anyone involved in the electronics industry. From the types of resistors and raw materials used to the intricate manufacturing techniques and quality control measures, each step in the production process contributes to the reliability and performance of these components. As the industry evolves, staying informed about future trends and advancements will be crucial for manufacturers and engineers alike. The future of chip resistor technology looks promising, with ongoing innovations set to enhance their capabilities and applications in the ever-evolving world of electronics.